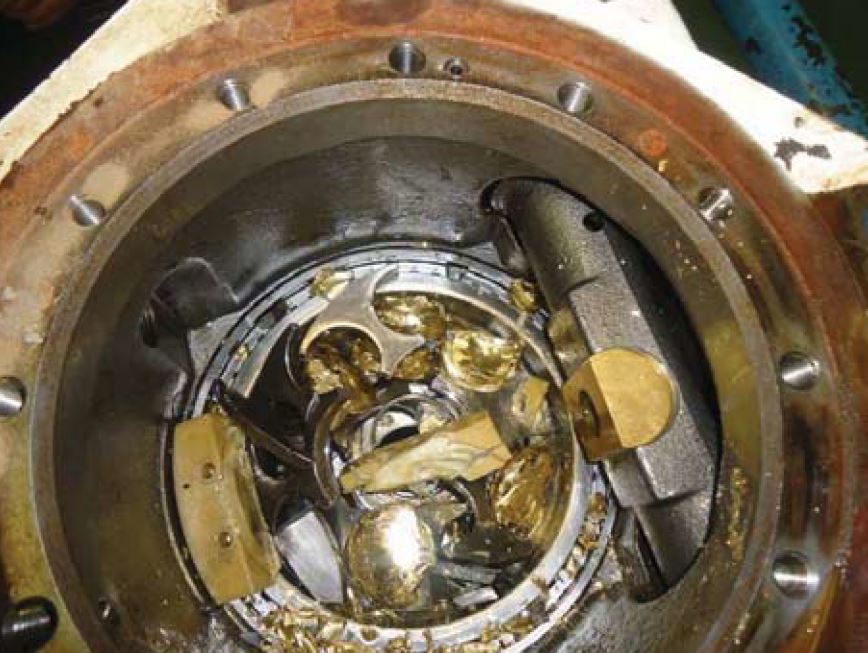
Research has shown that more than 75% of hydraulic system failures occur from system contamination. Machine builders, equipment maintenance managers and operators must pay close attention to factors which affect the cleanliness level of hydraulic oil in order to minimize lifetime costs. However, even if operators are diligent and have rigorous maintenance procedures in place, it is almost impossible to remove all contamination from a system. For example, contamination may lodge in a corner of a fitting during machine assembly. After flushing prior to startup, this contamination may remain in the system if it is located in an isolated area away from the main flushing flow. Contamination such as this can work its way into the main system flow throughout the life of the machine due to different reasons such as machine vibration, the heating and cooling of the system, movement of the machine etc. Contamination is also constantly being generated internally during machine operation. For example a piston motor can generate metallic particles while starting under a heavy load before a lubrication film forms between moving parts.
The most effective way of minimizing system contamination and lifetime costs is through intelligent system design. Proper selection, sizing and placement of the numerous types of filters and oil conditioning equipment available can contribute enormously to the health of the hydraulic system. A well designed system will maintain high levels of oil cleanliness despite the numerous sources which can produce contamination.
The critical sizes of dirt particles for hydraulic systems lie in the range from 0.2 to 100µm. In comparison, the minimum particle size that can be seen with a human eye is approximately 40µm and the width of a human air is around 75µm. The ever increasing operating pressures of hydraulic systems beyond 350 bar leads to tighter dynamic tolerances of the internal working parts of hydraulic components. As tolerances become tighter the cleanliness level of oil needs to increase. Smaller dirt particles become more problematic in relation to the gap between moving parts.
What are the effects of contamination in the oil? Contamination wear generally falls under four categories:
- Abrasive wear – dirt particles between reciprocating surfaces leads to an abrasive wear of the surfaces. This can affect component tolerances, lead to increased leakage and generate additional particles which leads to more wear.
- Adhesive wear – high loads, low speed or reduction in fluid viscosity can lead to contact of metal surfaces which it turn can cause cold welding or component wear.
- Erosive wear – where there are large pressure drops and as a consequence high localized oil flow velocity, particles entrained in the oil can cause an erosive wear pattern on metal surfaces. As a result parts lose their working tolerances and form.
- Surface fatigue – particles between two surfaces can cause high local contact forces causing pitting, leading to further particles being entrained into the system.
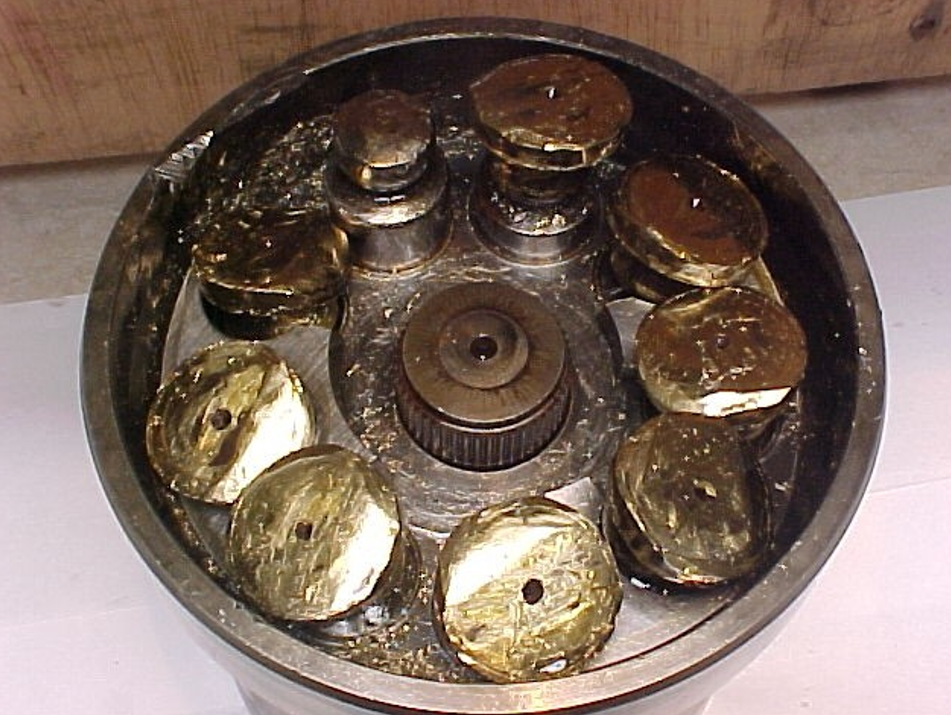
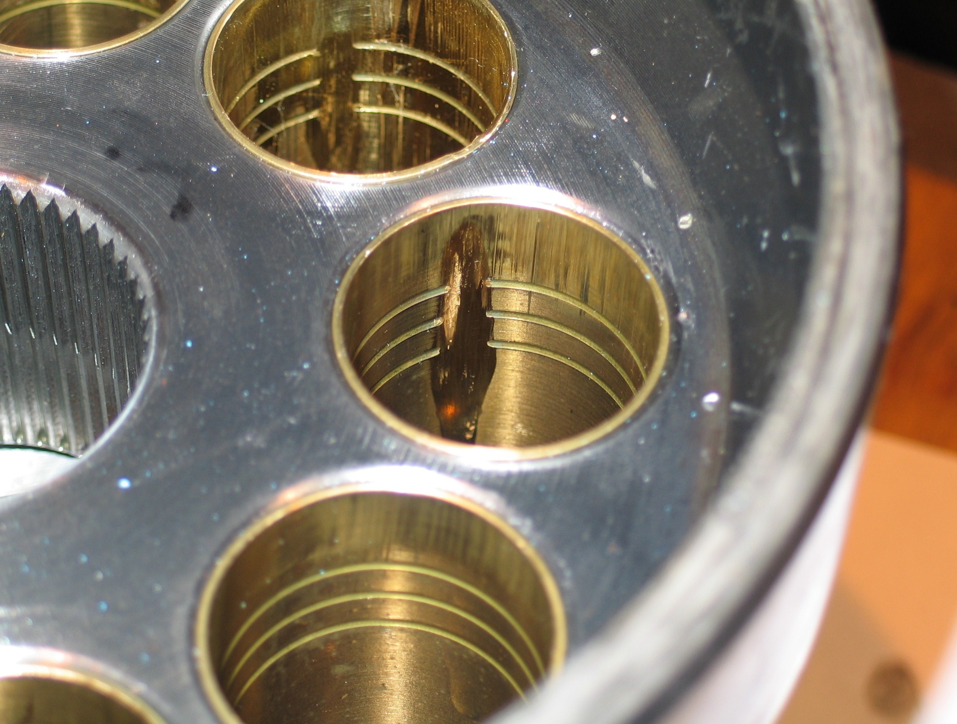
What are sources of contamination? There are many sources of system contamination including:
- During initial assembly dirt can be built into the system.
- While maintenance is being carried out, dirt can migrate into the system while components are being replaced or adjusted.
- Dirt can enter the system through leaking suction lines.
- Dirt particles are present in the air which is worse in certain dusty environments. Poor selection of air breathers can allow this dust to make its way into the hydraulic tank.
- Cylinders can be a significant source of contamination as the rod surface is exposed both to the external atmosphere and to the oil in the hydraulic system, as the cylinder is extended and retracted.
- Refilling the system with dirty oil. In general, bulk hydraulic oil delivered from the refinery needs to be filtered before it goes into the hydraulic system.
- Moisture in the air can make its way into the system through the tank breather.
- Internal wear of hydraulic component parts.
As stated above, intelligent system design can go a long way to minimising contamination problems. Some important considerations when selecting filters and designing the system are:
- The use of pressure filters is advisable when the system contains sensitive components such as servo valves. They should also be considered when a system shutdown will have high economic consequences.
- Pay close attention to filtering of boost, flushing and servo flows. Filtering of case drain flows should also be considered. Some manufacturers strongly recommend this for certain products, while other manufacturers advise against filtering case drains or to filter with extreme caution.
- When selecting return filters, care should be taken to size the filter according to the maximum possible return flow. This may be larger than expected due to differential areas of hydraulic cylinders for example.
- The use of offline filters can have a major effect on the cleanliness level of a system. Even though the flows involved are typically very low, the constant flow through this type of filter can significantly reduce system contamination.
- When designing the tank, ensure the return connections are relatively far away from suction connections and that they are separated by baffles. This allows air and particles to settle out from returning oil before it is pumped back into the pressure lines.
- Use of minimess points to allow connection of measurement instrumentation or to allow an oil sample to be taken. This minimises exposure of the system to external contaminants.
- Use of quick connect couplings to fill the system with new oil. Again this minimises particle intrusion.
If you need support with minimizing contamination in hydraulic systems, you can contact us here: https://antares-global.com/contact/